Introduction |
Like most of you in the US (and elsewhere) who are somewhere near my age (B.1948), I read all about Cook Neilsen and Phil Schilling’s escapades with Overdog, aka Old Blue. I got hooked on Ducatis and in ’75 bought a leftover new ’74 750 GT. In ’76 I moved to California to pursue both a better job and more time to ride and got to watch Cook race at Riverside, Sears Point and Laguna Seca, along with Kenny, Eddie and Freddie. Amazing stuff that made me want to race desperately. But then again I had wanted to do that since I was 17. Hailwood was God to me. I was nearing 30 at the time, but making a good living as a chemical engineer in the pharmaceutical industry at Hyland Labs near to Glendale. Because of the GT and a burned exhaust valve, I met Jim Woods, who was just getting his shop going in Glendale. He convinced me that he needed to fix the problem and a friendship began. After awhile, I joined the group of hangers-on at the shop and we started riding the Angeles Crest Highway twice a week. My poor GT had trouble keeping up with the 750 sport of Jim, and 850 Lemans’ of the other guys and in ’78 I bought a 900 SD Darmah. Suddenly I found myself leading the pack, by a lot. Jim decided he needed to build up the shop’s reputation as a performance oriented place and felt that going into the local club-racing scene would be a good way to get started. He approached me about being the rider as long as I would help put the bike together and maintain it. He would provide the shop, parts and his mechanical know-how, which was considerably more than mine. Our first racer actually was two Darmahs that were crashed insurance write-offs that Jim acquired. We put the best of the two together and I began learning the club circuits of Willow Springs, Ontario (now gone), Riverside (also, sadly gone), and Sears Point in the AFM and ARRA. I was very green, but old enough not to be too stupid. I was a slow learner, but the lessons usually stuck. It quickly became apparent racing against the Japanese bikes that yes, the Ducati handled better, but was really down on power. So you had to ride really hard in the corners to make up the lost ground. Over the next few years until I stopped racing in August of ’84, the search was for power and reliability. I had reasonable success for an amateur racer, winning a few class championships and placing well in national BOTT races, as long as the bike held together and I didn’t do anything too crazy. I never considered myself one of the really fast guys, just a fairly fast club racer. Getting passed at Warp 9 by Freddie on the banking at Daytona in Superbike practice is really humbling. Now I should caution everyone that what I have learned about building a Ducati racebike and engine modifications is A way of doing things. There are probably many other ways. I think that I have learned to be somewhat open-minded about this. Jim Woods started out the racing project with a lot of good ideas. I went along with them until Jim introduced me to C.R. Axtell. He and Mike Libby, his partner, repped Dell’ortos at the time and did some headwork for Jim, like making valve guides and putting in new seats. I had read about Axtell. He was always referred to as "the legendary" in the cycle magazines. I quickly found out why. During the rest of this I will refer to Ax frequently for very good reasons. Apart from his role in providing some of the HP that has been so important to many a race winner he is just one very smart and engaging guy. I have been fortunate enough to be around good and even great scientific people for most of my career. He would put most of them to shame. He is now semi-retired and we talk occasionally on the phone, usually about jazz. He designs camshafts now and has done work for some of the big car racing teams and builders.
|
The
Engine Cases, Crankshaft and Oil System |
I have grouped these together because they sort of work hand-in-hand. Most of you already know from reading about Neilsen’s bike and probably some of your own experiences that the Achilles heel of the built-up bevel drive engine is the roller crankshaft. It will fail about every 4-6 hours in racing conditions. (My 750 GT with its nicely underpowered engine had the same crank for 110,000 miles, I even wore out the angular contact main bearings at 94,000-the phenolic cages disintegrated!). All of my racing cranks were put together by Jeff Bratton, who may be the best roller crank guy around. They were all balanced by Hank-the-Crank in North Hollywood. A 53-55% balance factor was used. My racing cranks would fail just like everyone else’s. I tried different kinds of oil, settling on Redline 20w-50, which played havoc with the clutch because it was so slippery. But that didn’t really help the crankshaft. Jeff Bratton would always call me upon receipt of the latest trashed crank and new rod set and say, "Kevin, these bearings on the old rod set are purple. This thing isn’t getting any oil." For reasons that are not clear to me (stupidity?) I didn’t go to Axtell with the problem until much later. In the meantime I tried first a simple roller crank conversion that I obtained from Albert Bajohr in Germany, who I met at Daytona in ’83. That stopped the crank failures, but later I went on to a complete changeover to Carillo rods and my own pin. More on that later.
Now the basic engine design is good and by all viewpoints the crankshaft shouldn’t fail at the rate that it does. The sump carries over 4-L of oil! How come the crank is running dry? It is really very simple. Axtell looked at the internal case design and said, "Our Italian cousins are so smart in other areas, how come they made the drainback holes so small? The oil pump pickup is sure to starve. This oil has got to have a way to get back down away from all of these rotating parts. In addition to pump starvation that is lost HP." Look at it yourself. There are just a few small slots separating the sump from the crank and transmission cavities. Even hot oil just can’t flow down quick enough. The fix? Just drill a bunch of 3/8 in. holes in the pan below the transmission. The crank area has a weir (lip) in the cases that is designed to strip the oil from the crank counterweights and direct it back to this area. The pan just needs more holes to drain back to the pump pickup (See pictue below).
A simple way to improve drainback to the sump by enlarging existing holes and adding a few.
Now I went a little farther on my racing cases and widened the existing slots and oil pickup shrouding with a Dumore porting tool and put a screen over the drilled holes (See pictures below). This is common practice in wet-sump racing car engines. Roller cranks need oil volume. This fix is essential. Plain bearing cranks need oil pressure. The fix is not quite as essential if you convert to plain bearings as I did, but can’t hurt.
Right hand case and an attempt to improve oil pickup that was completely unnecessary. It uses a hot rod Chevy style lowered oil pickup epoxied into the case.
another view of the right side case drainback screen and holes.
How crazy can you get? Screen is supposed to damp out oil impact and minimize splashback to the upper case. Commonly used in sprintcar engines. Green stuff is 1838 3M epoxy... amazing stuff.
What else can you do to increase oilflow?
* Replace the unsealed bearing at the end of the crank with a sealed bearing. That will direct all flow coming to that cavity in the clutchside cover to the crank. This is by the way essential for a plain bearing crank to keep the oil pressure up to the 70-90 psi you need at full-on rpm. A sealed bearing has slightly higher friction loss than unsealed, but the trade is well worth it and the HP loss unmeasurable.
* Restrict the flow to the heads. Install smaller orifices in place of the dowels between the cylinders and heads that carry oil to the heads. Diameter (ID) we used for the roller crank was: 0.112 in.
* Block off the ball bearing relief valve behind the pump cavity.
* Some earlier cranks have a sleeve inserted in the end of the crank to restrict flow. Even the factory suggests removing that for racing.
* Last, and certainly not least in the way of work, is to redirect the head drains away from the rotating crankshaft. The stock head drains go through the cylinders and fall right on the crankshaft. All that oil hitting the rotating crankshaft just slows it down, somewhat like a waterwheel brake. That oil in-turn gets taken up by the transmission and this all both slows oil drainback and robs HP. Draining the rear head externally involves hacking up the fins in the cylinder so you can fit some Earl’s supply type fittings into the head drains and run braided SS lines down directly to the sump (see below).
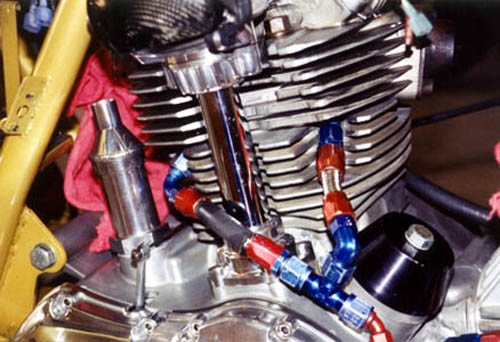
oil line routing from
rear head
|
* The front head
is easier. You just weld a fitting on the exhaust valve cover, then
run a line back to the case below the level of the crankpan (See
picture below). In
the overall scheme of things the oil just gets back down faster.
Meanwhile you get the extra benefit of an engine that spins up
faster because it is not fighting all that drainback oil. My bike in
the photos shows how this is done. Others have done this too. The
engine is definitely more responsive.
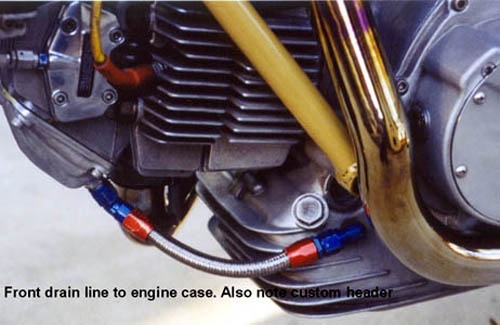
external drainline
using stainless steel braided line. Also good view of rear
header
|
The cases don’t take kindly to the
pounding of increased HP. They will eventually crack around the main
bearing webs. This is fairly well known. Inspect periodically. I
fortunately have access to an excellent welder. He lives here in San
Diego, and his name is Rob North. BSA/Triumph triple fanatics will
probably recognize the name. I don’t honestly know if welding serious
stress fractures of this type will work. Rob has welded my present
slightly porous cases in a number of minor crack areas (See pictures
below). They
look considerably better there than the original castings! The base
metal is not real good for welding. It is full of voids. You really need
to have someone who knows what he is doing with aluminum welding.
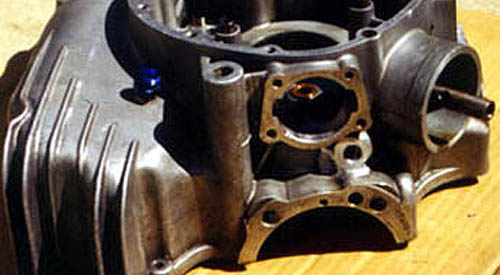
welded up boss
between fronthead cam drive tower casting and front cylinder
casting. This is standard factory location, but this set of
cases was porous, so Rob North had to fix them by filling with
weld.
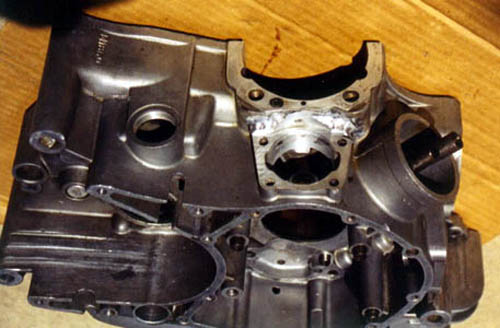
welding and remachineing
between rear cam drive casting and rear cylinder casting. This
was porous also and Rob North also welded up.
|
|
Crankshaft
plain bearing conversion with Carillo rods |
In my frustration with crank failures I
finally decided to go with a serious plain bearing conversion.
Fortunately, Ax had some leftover Carillo rods from a cancelled
flattrack project for Yamaha involving the Virago engine, of all things.
I am sure that this conversion can be done a number of ways, with a
number of different rod sets and pin diameters. After all, plain bearing
engines are the rule these days. There may be a few people out there
that even do this conversion as a kit. But at the time this wasn’t
common for Ducatis, and I had to figure it out as I went along.
Basically there are a few things to consider.
- Pin:
I designed a pin that mimicked the Yamaha Virago engine. Diameter is
1.9675-1.9679 in. Essentially the pin holes are horizontal (180
degrees) when the crank is out of the engine on the workbench and
sitting on the counterweights. The pin feed hole is 0.200 in and the
four holes to discharge to the rods are each 0.175 in. Now there has
been a lot of research done by people on the best place to put the oil
supply holes to counter the pressure of the piston on the power stroke
and the hole diameter. I figure these people know a lot more than me.
But I did reduce the hole diameters slightly (0.025) from Yamaha’s.
I used 6150 steel, heat treated to Rc of 58-60 for the pin
material based on a recommendation from Jorgensen Steel’s technical
guru and my 75 year old German machinist friend Otto, a master
craftsman, talked about in hush tones among LA machinists. Otto made
the pin according to my drawing and San-Val, probably no longer in
business, did the pin grinding after heat treating. There are
certainly other steels that can be used. A sketch of the pin is
available from me. (In Jan. 2002 the pin fractured cleanly in half. It
was heat treated too hard, or more accurately, through-hardened when
it should have been case-hardened. I also had not made sure that
radiuses were ground into the step change diameters when it was
originally made. Sharp corners create stress risers that ultimately
lead to failure. I have made a new pin of 4340 case-hardened to Rc
53).
- Bearings:
Since the rods and pin were set up for the Yamaha engine, I had a
ready supply of bearings in five thicknesses. Basically any hot-rod
automotive book tells you to set up the bearing clearance at about
0.001 per inch of pin diameter. This is a general rule of thumb.
- Rods:
Carillo, one of the most highly respected names in performance rods. I
used a shorter rod than the stock one. 5.550 in. vs. stock 5.709
(145mm). This gives a rod/stroke ratio of 1.89 and should give
slightly better acceleration of the piston to achieve better cylinder
filling compared to the 1.95 of the stock engine. Ax also had a longer
rod, but suggested we go with the shorter one. The primary reason is
to build toward the Ducati’s strength. That is torque down low. A
longer rod will allow the engine to wind up higher, but reduce the
torque at lower rpm. Since the Ducati is not a high revving engine by
design, Ax suggested building for a broad power band. Now if you look
at some of the books on car engines. Bill Jenkins, "The Chevrolet
Racing Engine" and Waddell Wilson’s "Racing Engine
Preparation, you will find a similar line of reasoning. I have found
both of these books to be invaluable in learning about engines.
This change also requires machining
the base of the cylinder to compensate for the shorter rod. Since the
difference in rod length was 0.159 in., then that should have been the
amount that needed to come off the stock cylinders. Mine were a little
shorter for reasons long ago forgotten. But I set things up for about
a 0.065 in. deck height by machining off 0.149 in. See the Piston
section for more on deck height.
Normally big end side clearance is
set up at 0.014-0.024 in car engines. Motorcycles appear to be able to
tolerate a little less. The S-2 engine which I later copied in oil
orifice sizes and big end clearances has a factory spec of 0.004-0.012
in. I eventually settled for 0.008 in. For comparison a 750 Paso is
0.0059 to 0.0138 in.
One other aspect about using the
Carillo rods is the need to machine the counterweights to clear the
rod main beam. The Carillos are a lot wider than the stock rods (See
pictures below). This requires serious amounts of balancing material (aka Mallory
metal) to counteract that removal of metal. Also the cases need to be
relieved at the bottom where the weir is located to allow for
clearance of the rod bolts.
Lastly, the rod assembly instructions
from Carillo are absolutely first rate.
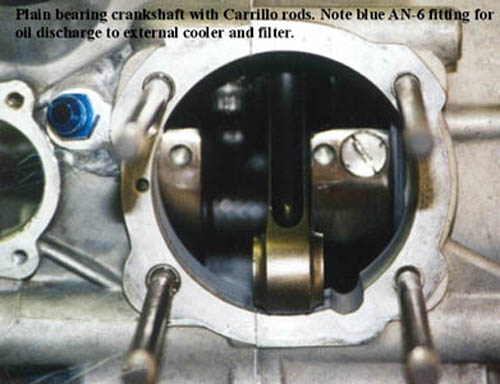
assembled plain
bearing crankshaft with Carillo rods installed in engine. View
from front cylinder, showing external oil feedline fitting at
left (in blue)
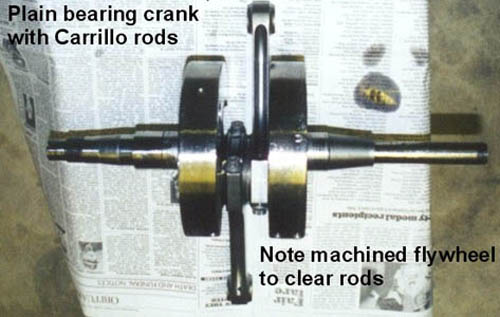
plain bearing
crankshaft with Carillo rods. Note that inner surface of
flywheels are machined to clear rods.
|
- Oil Pressure:
The main reason for tightening up the big end side clearance was to
get the oil pressure up to the Carillo and Axtell recommended figure
of 70-90 psi hot at maximum rpm. This should be about 10 psi/1000 rpm.
So at idle, I read 10 psi. At cold startup the engine hits 90 psi and
then settles down. The Ducati’s oil pump is designed for a roller
bearing application so it is on the ragged edge for supplying the
needed pressure. At first I blocked off the stock oil filter, but more
recently because of concerns about getting oil to the bevel gears I
put a small orifice (~0.040 in) in the base of the filter holder tube.
I drilled into the boss cast into the cases in between the front
cylinder and bevel tower drive (see below )
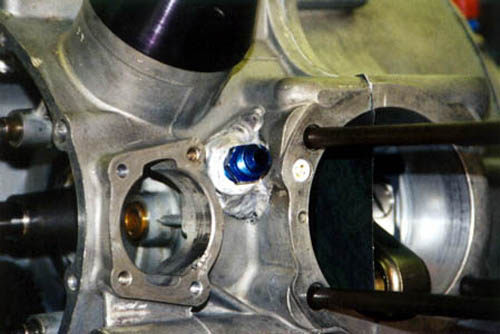
fitting
installed into external oil feed hole
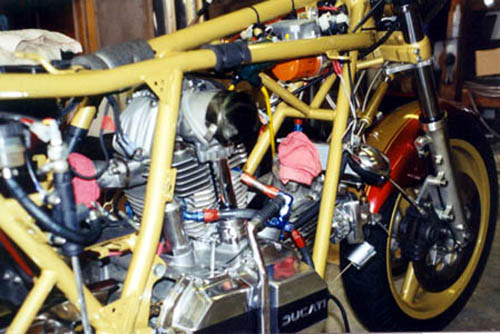
Clearer view of extra tubes welded to lower headstock
and main frame backbone to control headshudder under heavy
braking.
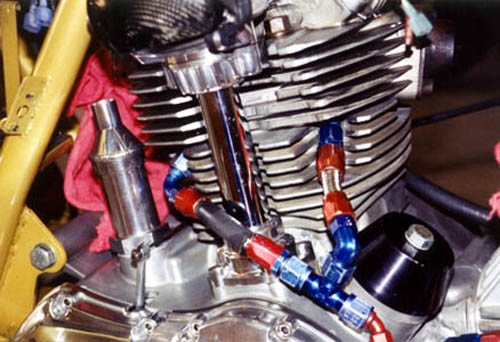
oil line routing
from rear head
|
ran a braided SS line
up to an Earl’s external oil filter holder that I mounted under the
gas tank, down to an Earl’s oil cooler mounted to the front intake
valve cover like a Monster (see below)

mounting of oil
cooler. Don’t recommend this method. It leads to cracks in
the cooler. I have since switched to the Earl’s brackets that are available with their coolers.
|
and then up to an external manifold
with four outlets (see below)
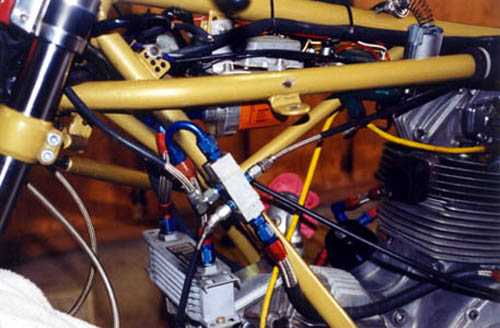
crowded picture showing
manifold for external oil feed distribution to both heads,
crankshaft, oil pressure gauge. Can also see oil cooler
mounting, extra welded in frame supports to minimize head
chatter during braking (Steve Wynne suggestion). External Earl’s
mounting block with oil filter.
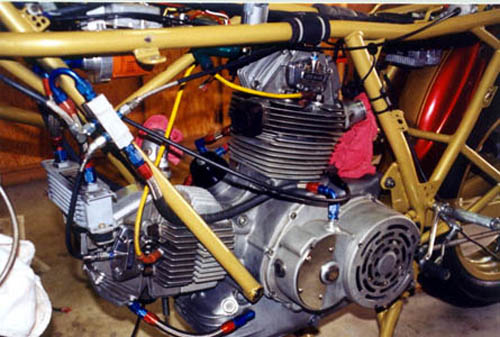
complete view of
Left hand side oil line routing and Vee-Two dry clutch.
|
Two are –3 SS braided lines restricted
with #65 pilot jets drilled out to 0.041 in. to feed the heads, one
–4 braided line goes to an oil pressure gage mounted on my
instrument panel and the last one, a braided line, goes down to
the crankshaft via the clutch side housing. All this external plumbing
requires machining the head cam end caps for –3 fittings and
machining and welding the clutch cover for the oil feed line (see pix
below).
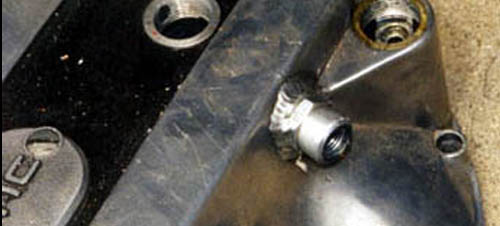
one way to weld a
fitting into the clutch side case cover to install an external
oil feed to the crank.
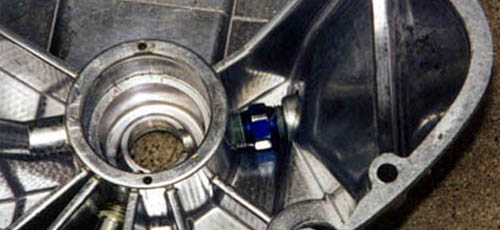
the interior view
|
You must also not forget to block off the internal case feed lines to
the heads and crank. All of these dimensions and feed line changes
were arrived at through an arduous process. I will not describe the
details. I did use an external adjustable pressure relief valve at
first to ensure that I did not overpressurize the system, but once I
had everything working properly I removed it.
- Oil pump:
I use the stock pump with the usual round screen strainer in the
cases. The pump is speeded up with Albert Bajohr’s gears. Stock
gearing is 22T on the crank and 51T on the pump, while Bajohr’s
gears are 47T and 26 T, a ratio change from 1:2.318 to 1:1.808. I read
recently in one of the Bevelhead posts that a Mille pump will fit the
engine and has better capacity. That would be an easier fix. I will
have to look into that myself.
I have disassembled the crank for
inspection on numerous occasions after dyno runs and after a few
thousand street miles. Everything appears to be working quite well. |
Pistons |
This is the key power element in the Bevel
drive engine. In December 1980 CR Axtell let us bring our near-stock
Ducati in for a dyno run. My dyno run sheets showed that with 40’s,
Conti’s, stock valve sizes, porting and valve job by Jim Woods and
standard Nippon-Denso ignition the bike made 59.6 HP. The dyno table is
shown below. The first HP column is with stock cams. Later in January of
’81 we ran the bike again, but this time with the "Imola"
cams. Note that the stock cams are actually better for street riding.
They are geared to the engine’s strength—torque down low. The Imola
cams give less power down low and only make a really big difference at
and above 8500 rpm, dangerous territory for the crankshaft. I remember
quite painfully ($$$) the result of racing with consistent shifting
above 8500 rpm. Usually in the next race, the crankshaft would fail,
taking the pistons with it.
Near-stock 900SS engine,
CR Axtell’s dyno
|
Stock cam |
Imola cam |
Rpm |
HP |
HP |
4500 |
47.0 |
42.3 |
6000 |
57.3 |
56.0 |
7000 |
59.6 |
58.0 |
8000 |
55.4 |
54.6 |
8500 |
45.0 |
54.2 |
9000 |
Not run |
46.6 |
Note: all values are corrected to standard temperature and pressure at the time of the test
After seeing the unimpressive results
on the dyno, Ax took pity on me. He suggested that some good high
compression pistons would do wonders. He was right. I was to find out
that this was typical advice from Axtell…being right, that is. Having
had many a piston made in the US, Ax was not particularly happy about
their longevity and quality control. He felt that the aluminum alloys
used by the American piston manufacturers were not high enough in
silicon and thus too soft, leading to dimension changes under the stress
of racing. Ax suggested Europe or Japan, with Cosworth as a possibility.
Luckily, Cosworth had a local site in Torrance in the early 80’s. I
approached them and to my amazement they were willing to make me a few
(3) prototype pistons. I drew something up and Ax corrected my
misconceptions. I sent the sketch to Cosworth. It was an 87 mm diameter
piston that increased the displacement to 883 cc. Ax was pleased. After
some nervous moments on my part wondering if they would ever get here,
Jim Woods installed the pistons (see below) and we ran on the dyno again.
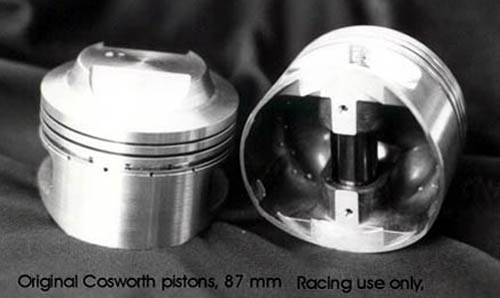
original Cosworth
pistons Axtell helped me design.
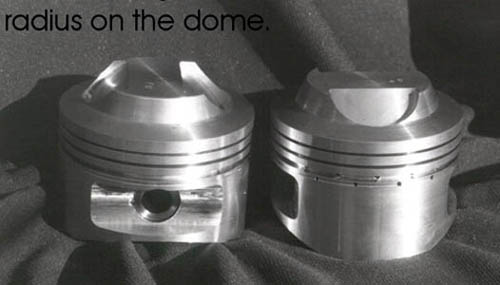
another view Cosworth
pistons
|
Basically, just installing those pistons yielded 80 HP. Here is the
chart again with the previous numbers side by side for comparison. The
Cosworth pistons were tested with the Imola cams. I think I jumped all
around the shop. When I got to Willow Springs Raceway, that change was
worth 4 seconds a lap.
|
Stock cam |
Imola cam |
Cosworth pistons |
Rpm |
HP |
HP |
HP |
4500 |
47.0 |
42.3 |
Not run |
6000 |
57.3 |
56.0 |
68 |
7000 |
59.6 |
58.0 |
76.6 |
8000 |
55.4 |
54.6 |
80.2 |
8500 |
45.0 |
54.2 |
78.7 |
9000 |
Not run |
46.6 |
72.5 |
Deck height:
This and the clearance of the valves to the piston cutouts should ALWAYS
be checked on first assembly of new pistons or cams. That includes any
other change that might affect the piston-to-head clearance or
piston-to-valve clearance on overlap. This is most easily done using
strips of soft solder taped in place in the squish band areas and valve
pockets. This allows something solid, but easily deformable that you can
check with a micrometer and is not prone to the distortion you can get
with clay. The closest I ever ran was .040 in. (1 mm). This is the usual
stock setup, but if you are spinning your engine above 8000 routinely,
you may get some piston to head contact from crank flex. There also may
be a contribution from expansion from thermal growth of the aluminum,
but that should be minor because of the steel studs and connecting rod.
It doesn’t take much contact and your crank and pistons are trashed. I
usually played it safe with an extra 0.010 (0.25mm) or more clearance.
This can be adjusted by machining the squish band area of the piston or
using extra or less base gaskets. Bill Jenkins book, "The Chevrolet
Racing Engine" covers this. He indicates that deck can be increased
to as much as 0.070 in. without a measurable power loss. I have run as
much as 0.065 in. and didn’t see much difference, but these are much
smaller engines and may be more sensitive. Waddell Wilson’s book,
"Racing Engine Preparation" sets 0.040 in. as a hard limit.
For what it’s worth, my best dyno runs seemed to coincide with tighter
deck heights than 0.065 in., say 0.040 to 0.050 in. or so. But we were
usually changing other things at the same time, so I am not sure that is
the sole reason. Axtell’s personal opinion about this is to run as
close to 0.040 in. as possible, even tighter is better. He used to run
0.037 in. with Triumphs. A lot depends on the flex of the crank. With
the stepped pin of the later cranks, and certainly the plain bearing
conversion I have done, that is eliminated to a large extent.
During the course of the year as more
was understood about the piston and combustion chamber interaction, the
piston dome shape was altered slightly to control detonation. The change
was to radius the dome on the spark plug side. We were getting
detonation because the sparkplug was too shrouded. This was seen because
of the condition of the plugs and the fact that the base gaskets would
blow out (ooze, really) of the cylinders. I remember almost getting a
heart attack when Ax told me to file the dome and I carefully took about
1/64 of an inch off. He said "no", he would show me. He then
took a huge aluminum file (large space between the teeth) and quickly
filed away about 1/8-1/4 of an inch from the spark plug side of the
dome. My Cosworths!! But it worked. The detonation was gone forever.
Later on I had Cosworth draw up an 88
mm piston. I still have the drawing for those pistons, but their price
was too high for me to afford making up more than a few. I wanted to
sell the pistons as a way of supporting my racing. After a while we
tried JE, who in Ax’s opinion was the better of the American
manufacturers. However, we introduced something that he had tried in the
past with some success on his own projects. In the 50’s the aerospace
industry was having a problem with post-forging distortion of aluminum
parts. Some really bright people came up with a method of stabilizing
aluminum parts such that the distortion would be minimized. Going into
this in any detail gets into a technical area of structural mechanics
and stress relieving that I don’t begin to understand. However, I did
read the original published papers in a trip to Caltech’s library.
(Being a chemical engineer does help somewhat). Basically the method
involves using liquid nitrogen in combination with heat cycling to
stress relieve the parts from forging and heat treatment stresses by a
simple immersion process. There were a number of places that could be
done in LA. It apparently works pretty well. We used it on the JE
pistons prior to machining and that appeared to allow them to hold their
shape considerably better than we expected. We checked skirt dimensions
just about every second or third race. Too much clearance would lead to
all kinds of problems with blow-by past the rings and poor heat transfer
to the walls. Although the JE’s did not maintain their shape as well
as the Cosworth’s, they were acceptable. By the way, liquid nitrogen
stabilization has become the rage in the rifle industry to control
barrel distortion.
A lot has happened in piston
manufacture in the intervening 20 years. I should point out that the
custom-made JE pistons I have in my Ducati now after 4500 miles show not
a scratch on the skirts. Except for carbon on the domes and a nice tan
color underneath, they look brand new. These were not liquid nitrogen
stabilized. Apparently some progress has being made. My racing pistons
never looked that good.
Returning to the development story...
In the search for more and more power we increased the displacement with
88 and then 89 mm pistons (905 and 926 cc). Generally, I would say that
with the pressed-in liners you really should limit the piston diameter
to 88 mm. At 89 mm, ring sealing seems to become a problem, primarily
because the liners get too thin and distort unevenly as they heat up. I
tried many kinds of liners, boring with deck plates, stabilizing the
cylinders, different ring packs etc. to try to solve that problem.
Nothing was really effective. So we kind of gravitated back to the 88’s.
Unfortunately, JE’s blanks at the
time were lighter at 89 mm than at 88. The 88’s required some serious
milling of the interior of the piston and judicious grinding around the
pin bosses to remove the excess material. The 89’s were considerably
less work. Stock Ducati piston weight is about 353 g. I had high
compression pistons ranging from 380 to 439 g. However I always
lightened the over 400 g pistons to less than 400. Usually about 390 g
was the best I could do. This was with proper training from Ax on what
metal could be removed and what was sacred.
HP with the standard 80 degree bevel
heads never exceeded 83-85 or so on Axtells’ dyno, however with both
headwork and pistons we did manage to progressively broaden the power
band. Strangely, I can’t seem to find any dyno sheets with numbers
above 83 HP, but I remember hitting 85 at least once. It is difficult
for me to separate the effects of headwork, piston design, exhaust
system and ignition timing on HP from this point on, because we usually
changed a lot of things at once. However, once the high compression
pistons made the big improvement in HP, any of these other changes were
really minor in comparison. I’ll get into that in more detail in the Heads
and other sections. In retrospect it is kind of amusing to me that we
tried so hard to find more power and the engine just did not really
improve a lot more. Still it was faster on the track. Every little bit
helps.
A few other items need more discussion:
|
Valve
Cutout and Valve-to-Valve Clearances |
You should have 0.060 in. (1.5 mm) on
intake and 0.090 in. (2.29 mm) for the exhaust on overlap. These values
are primarily to aid flow during overlap, not for piston to valve
clearance purposes. You should also have 0.060 in. between the valves on
overlap, although with the desmo head you can go lower. Ax has used as
low as 0.040 on some spring heads. I remember that Dale Newton’s
factory TT2 head had a valve-to-valve clearance of 0.025 in. Much of
what you can do here is limited by material available under the cutout
of the piston, cam design and the need to limit sinking the valve too
far in the head. If the piston does not allow the clearances necessary,
then sinking the valve(s) is an alternative. However in doing so, you
run the risk of cutting down on the margin available for a good
transition in the valve seat, which can negatively affect flow, as well
as increasing head volume which lowers compression ratio. |
Cylinders |
I tried all manner of cylinder liners. LA
Sleeve works ok, or did at the time. If severely damaged, the factory
liners can be removed from the cylinders by heating in a >450 °F
(232 °C) oven. New liners can be installed the same way. I think the
best way to go is the S2 (Mille) cylinders. They are all aluminum with
the Nikasil style surface. No conventional honing required. With
this type of cylinder now found even in dirt bikes, there are places to
get them resurfaced and diamond honed if something disastrous happens.
The improvement in heat transfer from using a completely aluminum
cylinder with no liner should be obvious. For those who want a detailed
understanding, refer to any book on heat transfer, (Kern, "Process
Heat Transfer" and Carslaw and Jaeger, "Conduction of Heat in
Solids"). I will be glad to discuss this with anyone who really
wants to know (trust me, you don’t). The key element in running the S2
cylinders is that the piston clearance must be tightened up
substantially compared to the factory or aftermarket liners. JE
recommends running 0.001 to 0.0015 in. cold clearance with Nikasil
style cylinders. Normally with cast iron or steel liners, the clearance
is more like 0.0035 to 0.0045 in., or even more, depending on the piston
manufacturer. (They always make a recommendation with their own
pistons). The tighter clearance requirement is because the S2 cylinder
expands at the same rate as the piston, whereas the cast iron type
liners don’t. Too much clearance once the engine warms up and you get
a lot of blow-by into the case from the combustion chamber and a loss of
HP.
One other issue about the S2 cylinders
is the needed to run cast iron rings, or more specifically, NOT run
chrome rings. Again, compared to 20 years ago, the piston manufacturers
have this "minor" item figured out. JE uses Hastings rings and
they seem to work well. |
Compression
ratio |
We ran a variety of compression ratios by
altering dome height, but mostly the engine turned out about 12:1. That
is what I am running now in my streetbike. It might surprise you that
American street gas (92 octane) can run without knocking, but Axtell has
done dyno tests, which certainly stress an engine far harder than street
riding or even racing. Present-day pump gas can handle that level of
compression with no problem, and just as importantly, no significant
difference in power compared to racing gas. I am not particular about
the kind of gas I put in the engine, although Axtell’s testing seemed
to show that Super Shell was slightly better than the others for power.
Of course, he was limited to gasoline brands available in California.
Until you get much over 12:1, say to 13:1 or so, race gas (>100
octane) just isn’t needed. |
Heads |
Of all the things to do for the engine
this is by far the most work. On the standard heads, quite honestly, the
smartest thing you can do for yourself is to get the best valve job you
can find. Do not waste money on even cleaning up the ports. The HP gain
is just not worth the effort. Basically the port design with the 80
degree included angle in the valves is just beyond correction without major
surgery. Some people have tried "D" ports with some
success. Jim Woods suggested that when we just weren’t making any
progress with the standard bevel drive heads and we did install some
aluminum D inserts in the exhaust ports. That helped some, but we are
talking about really small improvements.
On Axtell’s flow bench the ports are
tested with a simple manometer measuring pressure differential in inches
of water that can be converted to flow. Many flow measurement devices
use this principle. The conversion to flow is rarely done at Axtell’s
because that is just another way of expressing the pressure
differential. So most of the flow bench numbers I have are in inches of
water. I do have some conversions, which I will show later in the
section. But first let’s look at the best the standard, but modified
bevel heads did for us on the dyno. I’ve also included my friend Tony
Guest’s bike, a 750 SS (actual 905 cc), which was setup almost
identically.
My notes show the engine with the
following setup.
- 89 mm JE pistons
- Daeco race gas (104-105 octane)
- 150 main jets front and rear
- 30 degree spark advance (usually
required because ring sealing was not so good on the 89 mm
pistons)
- Dyna ignition driven off the rear
camshaft using a modified Lucas-Rita housing
- Deck height 0.040 in (1 mm)
- Megaphones (probably Bassani at
that time, my notes aren’t clear)
- 33 inch long, high-pipe headers
measured around the outside of the bends
- 40 mm Dell’ortos with long Dell’orto
plastic velocity stacks and huge K&N air filters (no
difference on the dyno with or without, but those expensive parts
are protected)
- Imola cams
- Heads: 44 mm intake and 36 mm
exhaust valves, "D" Port exhaust
|
’81 Cosworth pistons |
July ‘84
K Bracken
(89 mm pistons) |
June ‘84
Tony Guest’s bike
(88 mm pistons) |
Rpm |
HP |
HP |
HP |
6000 |
68 |
69.6 |
67.0 |
7000 |
76.6 |
78.7 |
81.0 |
8000 |
80.2 |
82.0 (82.8) |
80.6 |
8500 |
78.7 |
78.0 (82.5) |
78.4 |
9000 |
72.5 |
Not run |
78.0 |
Note: numbers in parentheses are the
best peak HP that I have charts on
Not much gain for 3 years of work. But
on the track the bike was definitely faster. We had some runs that
peaked higher and some runs that had more power at 6000 and 7000 at
different times over the years. My friend, Tony Guest’s bike, had very
similar numbers from an almost identical setup. His was a 750 SS bored
out to an 88 mm piston. Now we only really worked on the heads over the
winter, which is mercifully short (nonexistent, well, it rains
sometimes) in southern California. The rest of the time I was either
rebuilding a broken engine or just maintaining and racing. So don’t be
too misled about the time we all put into this. But we had to face that
we had hit a wall. We weren’t going to get much more power out of the
engine. So we decided to take the big plunge. This was about the time
that Ax would say, "You know how to drink Scotch don’t you? Well,
step over into my office." Which meant we were moving away from the
bench where he did all of his porting work and over to another table
about 3 feet away. This was where sketches would be made, serious
discussions would be had about port flow, good designs (XR750 and
Cosworth were "good" examples), poor designs (Ducati was the
"bad" example) and yes, Scotch would be carefully sipped. In
that state the time and effort needed to make a "good" port
would not seem so out of reach.
Before I forget, here are some flow
bench numbers. I will show a "stock" head or the closest thing
I could find in my flow bench sheets and the best racing head we had.
Everything is in inches of water. Only the Racing head was converted to
CFM. |
Standard
Ducati Bevel Drive heads: Comparative Flow bench numbers |
Valve lift
(0.001 in.)
|
Stock Intake
40 mm |
Racing Intake
44 mm |
Racing Intake Flow (CFM) |
"Stock" Exhaust, (early porting work)
36 mm |
Racing Exhaust, "D" Port
36 mm |
Racing Exhaust Flow
(CFM) |
100 |
0.20 |
0.25 |
N/a |
0.13 |
0.13 |
N/a |
150 |
0.43 |
0.63 |
N/a |
0.38 |
0.38 |
N/a |
200 |
0.80 |
1.00 |
107 |
0.50 |
0.63 |
85 |
250 |
0.88 |
1.25 |
120 |
0.75 |
0.88 |
101 |
300 |
1.12 |
1.50 |
132 |
0.75 |
1.00 |
107 |
350 |
1.30 |
1.63 |
137 |
0.88 |
1.13 |
115 |
400 |
1.40 |
1.75 |
142 |
0.88 |
1.25 |
120 |
450 |
1.50 |
1.88 |
147 |
0.88 |
1.38 |
126 |
500 |
1.50 |
1.88 |
147 |
0.88 |
1.38 |
126 |
Jim Woods had also tried a 42 mm Intake
and 38 mm Exhaust arrangement with Tony Guest’s engine. The flow bench
numbers were not much different and the dyno numbers as you can see from
the dyno chart above weren’t much different either. The "D"
port seemed to help the Exhaust more than the Intake, so we just did
that to the Exhaust. We actually bolted a contoured piece of aluminum
into the port to make the "D." Now it looks like we made some
decent improvement on the flow of both the intake and exhaust. But you
have to realize that Ducati Bevel drive ports are REALLY bad. Peak
intake flow on a good Harley XR750 flat-tracker was about 3.30!! Ax
typically gets in the range of 90-96 HP out of one of those engines
(2-valve, 750). We had a very long way to go.
Axtell has a simple calculation to
"predict" the performance of an engine on his dyno, based on
peak flow as measured on his flowbench. According to that, my engine
should have made about 84 HP. Pretty close, based on dyno testing. |
Converting
Belt Drive Heads to Bevel Drive Heads |
First I should say that this project is
not for the faint of heart. It is mega hours of work and could only have
been done by me with Axtell’s and his partner Mike Libby’s guidance
and considerable patience. The two-valve belt drive heads with their 60
degree included valve angle are an improvement over the standard bevel
drive heads, but they still need a lot of effort to make them reach
their potential.
Some of you may recall Dale Newton (and
Paul Ritter) from about the same time as Cook Neilsen and Phil
Schilling. (I was shocked to hear of Paul’s crash. I was in such awe
of him when he was racing for Dale). Dale passed away only a few years
ago. I am lucky to have counted him as a friend. We became close during
this part of the story. Dale could make friends easily. Although a big
man, he had an engaging, easy-going manner that quickly made you know
you could trust him and he would be there to help you in any way that he
could. And he loved Ducatis. About this time (’84 or so) the factory
was making the TT1 and TT2 bikes. As I recall, the TT1 had the 600
Pantah engine, and for the TT2, the factory bored and stroked the engine
to make it into a 750 with 88 mm pistons. Dale had a TT2 and was looking
for still more power. He knew that I had a very good relationship with
Ax, and Dale and I had talked at the races many times.
Dale had made some really good
connections with the Ducati factory and his business occasionally took
him to Europe. So he, Ax and I conferred and a wish list was made. For
this project the two most important things Dale was able to get were 2
sets of belt drive heads taken from the line before any porting or valve
seat work had been done and a copy of the machining print for the heads.
That was amazing. I never dreamed that I would have a copy of that
print. It certainly made things considerably easier as the project
progressed.
First, Ax had me take a used belt drive
head and port it out oversized in both the intake and exhaust. It was
the first time I had ever held a porting tool. That was the patience
part for Ax.
After some valve seatwork and initial
evaluation, Ax told me we needed to reangle the valves to get bigger
valves in and to aid in the recontouring of the port floors. This
reangling of the valves moves the lower edge of the valve into the port
floor. This creates more material to shape for a better flow contour.
The print that I had from Ducati and a machinist that Ax used on
occasion allowed this to be much easier than you might otherwise expect.
We reangled the intake valves 1 degree and the exhaust 2 degrees by
rotating from the tip of the valve in the normal closed position. We
then put in some dummy valve seats sized for 44 mm intake and 37.5 mm
exhaust (essentially Harley XR750 valve sizes. After that I spent many
hours contouring the ports where Ax told me and cutting the seats with
hand cutters where he showed me to. Eventually we moved to clay to
establish the best contour for the port. All along the way as each
change was made, I would measure things at the flowbench. Once we had
things looking good, where flow was a little over 3.0 on the flow bench,
it was time to move to the real heads.
That was where Frank Neimeyer came in.
I don’t know how Ax found this guy. He was in his early 20’s. Ax
used to call him "Frank Neimeyer, World’s Greatest Welder."
Frank would take the heads and almost completely fill in the ports with
weld. There was a hole about the diameter of a pencil when he was done.
And the heads were still flat and undistorted. For those of us who
consider welding a black art, Frank was just magical. He also filled the
original sparkplug hole so we could install a 12 mm plug. In retrospect
we should have done a 10 mm plug. That kind has become much more common.
I became one with the porting tool. You
might have expected to find some voids in the weld material that Frank
had put in the ports. No. It was solid. Now I was working for real, so
doing everything right really stressed me out. I was so worried about
messing up Ax’s spare Dumore that I bought one just to work on the
heads. Once I got things more or less opened up we put in valve guides
and seats for real and moved into the completion stage. Somehow I got
both Dale’s and my heads done. That is, I did all of the rough work
and then Ax would finish them up. His years of experience at this are
not to be taken lightly. Along the way each change was tested on the
flow bench (see below).
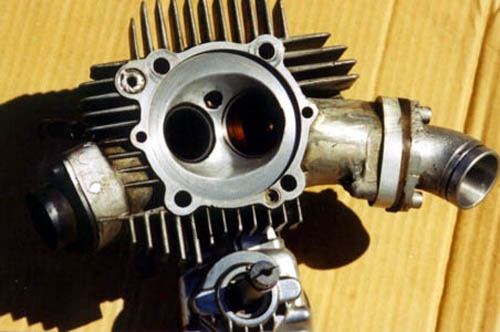
Front head, started out life as belt drive
casting. Reangled valves, welded and ported heads, 44mm In. 37.5
mm Ex Grafted on bevel drive. 12mm sparkplug, bathtub shaped
chamber. Fins removed from intake to minimize heat transfer to
incoming charge.
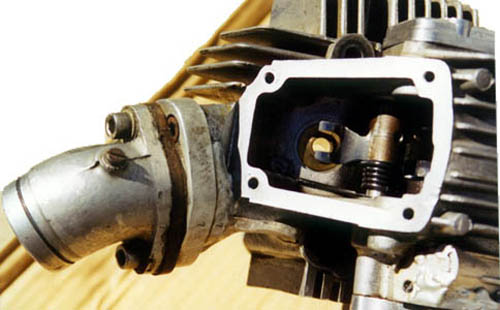
gives an idea how much we raised the port. Notice the
weld just outside the valve cover area. We also installed
oversize guides
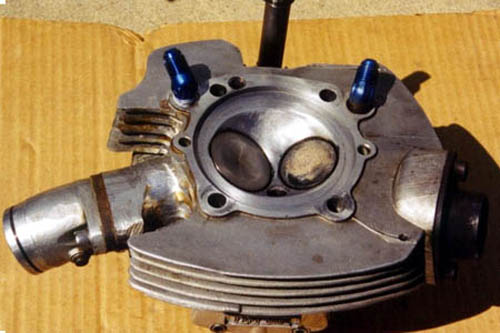
complete rear head showing , 45 degree fittings for
external drainback to crankcase. Chamber is same approach as
front head.
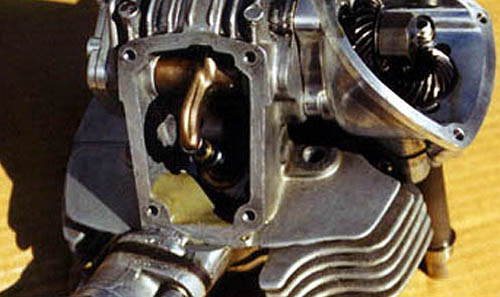
the rear head port came so high in the roof that it came
through even on these heads. This is a common problem in porting
the stock bevel heads. I filled in with epoxy. The front head
was discovered during early porting and I had it welded. The
rear head was not discovered until later. I was concerned about
dislodging the valve guides, so I epoxied. Works fine.
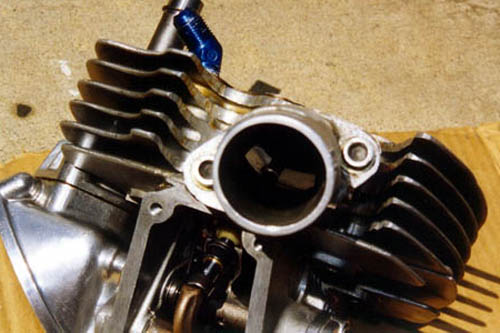
view down the port with valve open
|
Dale’s heads were the easy part,
basically a bolt-on when finished. Mine still had the problem of
grafting on the bevel drive system and the cams. With the aid of the
print and comparative measurements between the heads, it looked like the
drive adaption would not be too difficult. However, novice that I was, I
had no idea that the cams from the belt drive heads spun opposite to the
bevel drive heads. You work on one engine all the time and you start to
think that is the way all engines work. Not so. I remember driving home
from Ax’s one night and it hit me-- the racing cams from the factory
would not work. I had to have some cams made. Fortunately Jim Duer at
Megacycle was able to make desmo cams. I meticulously graphed out (1
degree increments) the factory racing cams and asked Jim if he could
match them, but in reverse. He said he could. Otto, my German machinist
friend, came to my rescue as usual also, by making a free set of
camshaft blanks that matched the bearings and spacings in the belt drive
head, but had the drive end of the bevel head. I just gave him a sketch
and he made them. Two of these (1 front, 1 rear) I sent to Jim Duer and
he then made the cams. I still have the drawings for the cam blanks.
The drive adaption was actually a lot
easier than I thought it was going to be. Fortunately with the ’84
heads (and for some time onward) the factory still retained the same
stud centers as the bevel drive engine. Basically the job was a
machine-to-match. The cam cap side required no changes. The drive side
required that the rear head be machined to match the head face to
centerline dimension of the bevel drive head and the front head required
the same. Because of the construction of the heads, the rear head
required the most material to be removed, while the front head only
required that the small ring protruding from the tach-drive casting be
removed. I used some 3M 1838 epoxy to fill in the extra space and bolted
the drives up (see below).
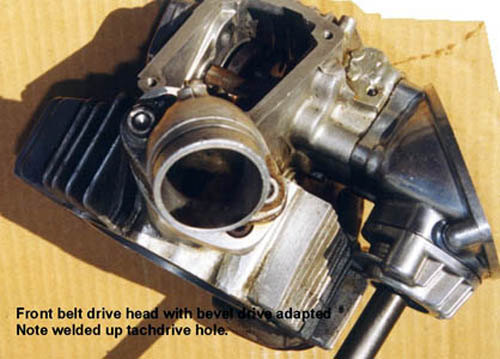
view into port and adaption of bevel drive to belt
drive head. Plugged and welded up tach drive.
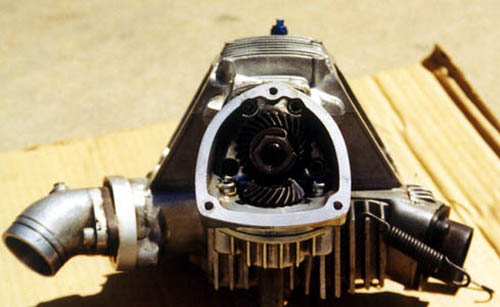
drive side view of attachment of bevel drive to
head. Bolt holes are same as standard bevel.
|
The holes for the lower socket head cap screws in
the bevel drive housings were too wide and had to be slotted inward a
bit to match the belt drive heads (see below).
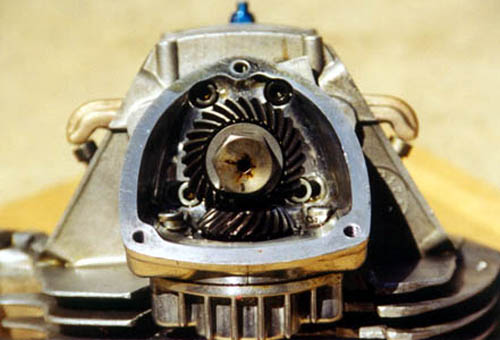
mounting of bevel
drive to belt drive rear head. Lucas Rita ignition drive nut in
place of stock cam nut. Note the slotted lower bolt holes needed
to get upper housing secured to head
|
Also because the cams had
different shaft diameters at various points than an equivalent set of
bevel drive cams I had to make up inner race bearing spacers as well.
That was about it. I’ve never had any problems with the drive
mechanisms.
Once I fired up the engine, needless to
say, I was concerned about how stable things would be in the heads. The
biggest problems lay with the cams. Apparently, to make the cams
Megacycle just flipped over the lobes of the racing cam profiles. This
doesn’t work because it slams the valves down on the seats too hard. I
graphed out the new cam profiles and found out that this was the case.
My valves would go badly out of adjustment in just one dyno run or one
race. Years later, when I resurrected the bike, I called Brook Henry at
Vee-Two. After talking about my situation I supplied him with all of my
drawings and the existing set of cams and he supplied me with a new set
of cams that has held valve clearance settings remarkably well.
Now what did all of this do? First I
will show the flow bench comparison with the best racing heads and the
heavily reworked belt drive heads. Then I will show what HP numbers I
have from the dyno at Axtell’s. Unfortunately, we never converted the
belt drive pressure differential numbers into flow numbers over the
whole range. I just have peak flow at 177 CFM. But you can get the
picture. It is interesting to see that the heavily reworked ports of the
belt drive heads don’t really show much until 0.250 in. lift. Then
things really take off. Peak pressure difference is 50% better than the
best bevel head on the intake and >90% better on the exhaust. (Keep
in mind that the conversion from pressure differential on the flowbench
is non-linear, so the actual peak flow increased only by about 20% on
the intake). Keep in mind that peak flow is not the whole story. It is
area under the curve, i.e. flow over the whole range of valve lift. This
was considerably better than before.
Valve lift (0.001in) |
Racing Bevel Intake
44 mm |
Belt Drive Intake
44mm |
Racing Bevel Exhaust
"D" Port
36 mm |
Belt Drive Exhaust
37.5 mm |
100 |
0.25 |
0.25 |
0.13 |
.25 |
150 |
0.63 |
0.63 |
0.38 |
.375 |
200 |
1.00 |
1.08 |
0.63 |
.68 |
250 |
1.25 |
1.56 |
0.88 |
1.00 |
300 |
1.50 |
1.90 |
1.00 |
1.43 |
350 |
1.63 |
2.18 |
1.13 |
2.06 |
400 |
1.75 |
2.45 |
1.25 |
2.50 |
450 |
1.88 |
2.68 |
1.38 |
2.64 |
500 |
1.88 |
2.82 |
1.38 |
2.64 |
The flow numbers are not quite up to an
XR750 Harley, but a lot closer than they were before, and a vast
improvement over the previous best racing heads. It looked like the
effort had paid off, at least on the flowbench.
In the earlier part of this section I
indicated that Ax had a rough calculation to predict the ultimate HP an
engine would make for a given air flow from his flow bench. Based on
that, Ax predicted that the engine should make about 100 HP. However,
dyno testing the engine was frustrating. The piston rings seemed to
refuse to seal. This created a lot of blow-by and forced me to run the
engine with about 28 degrees of advance. When I moved to the S2
cylinders it got even worse. The breather hose would spit oil all over
the back wall behind the dyno. Later on, as I described in the Pistons
section, I discovered that the clearance with the pistons had been
wrong. For the longest time I was convinced that the oil system was just
delivering too much oil to the cylinders because of the high oil supply
pressure and the oil rings couldn’t handle it. I couldn’t have been
more wrong. Now that I have the engine working properly I haven’t been
able to get up to Axtell’s in LA to do that "one last run".
But here is a tantalizing glimpse of what is there. This is a composite
of a number of runs done in 1986. Engine setup was with the Carillo
rods, 89 mm JE pistons, Northwest Sleeve liners, Barnett wet clutch,
Megacycle cams, 20w-50 Redline oil. The clutch slipped badly at 6000 and
the breather blew oil in a constant spray. After each run the valves
were seriously out of adjustment. Such is life. We had at least a 10 HP
increase, but we also knew that the engine was not working properly and
there was still a lot more potential.
|
July ‘84 K Bracken (89 mm pistons) |
’86 Belt drive head engine (89 mm pistons) |
Rpm |
HP |
HP |
6000 |
69.6 |
76.2 |
7000 |
78.7 |
85.2 |
8000 |
82.0 (82.8) |
93.3 |
8500 |
78.0 (82.5) |
91.6 |
We ran the bike at a Sears point
National BOTT race with Rich Oliver on board. He was in third place
midway through the race and the crank sheared off at the keyway on the
primary gear side. After repairing and trying a few other things to
contain the blow-by, we had Danny Coe race the bike at Laguna. He
finished in a strong 4th place. The overflow container could
barely contain the oil from the engine breather during the race. This
was obviously not a good thing.
During this time I also changed jobs
and started working in a start-up pharmaceutical company, divorced and
remarried, and started raising a second family. All of this made free
time to work on the Ducati almost non-existent, and truthfully, I was
getting burned out. I worked on the bike occasionally for a few more
years. My last dyno run was in December of ’89. No real changes there.
I then let the bike sit until ’96 when I decided to turn it into a
street bike. Now that project is "complete" (never is really),
I feel confident in believing that with no blow-by and a good dry clutch
I have somewhere between 93 and 100 HP.
Post script. My wife has a 2001 Honda
996 Superhawk, good for 101 HP, and 11.0 seconds and 125.2 mph in the ¼
mile according to Motorcycle online. In roll-ons from 60-120 mph., I
lose 1 bike length. (She is lighter than me!). Our bikes weigh
very close to the same. Mine is 418 lbs. "dry" (actual, with
oil, no gas) and hers is a claimed 423. So my resurrected ex-race bike
appears to be performing quite well.
|
|